DFMEAとは、D:design(設計)段階でのFMEAを指します。
Design Failure Mode and Effects Analysisの略です。
DFMEAとFMEAとの違いや、やり方、フォーマット&基準例などについてまとめました。
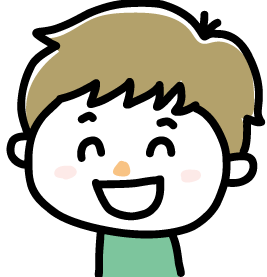
FMEAについてさらにくわしく確認したい方は、別記事でまとめていますので併せてご確認ください。
目次
DFMEAとFMEAとの違いとは?やり方やフォーマット&基準例
つまり違いは、DFMEAはFMEAの一部ということ。(設計段階)
DFMEAの範囲決定をするうえで、該当するコンポーネント、サブシステム、システムに関して考慮するポイントは以下のとおりです。
ポイント
- 製品はどのような工程、はめ合わせる相手部品またはシステムとインターフェースがあるのか?
- ほかのコンポーネントやシステムに影響を及ぼす製品の機能や特性は?
- 製品の意図した機能を達成するのに必要なほかのコンポーネントやシステムからのインプットはあるのか?
- 連結されたほかのコンポーネントやシステムの潜在故障モードを予防または検出する製品機能はあるのか?
考えられる故障や影響について洗い出しましょう。
DFMEAでの製造・組み立て性とサービス性(メンテナンス)の考慮
DFMEAで考慮すべき内容は、製造・組み立て性とサービス性(メンテナンス)に分けられます。
例を挙げておきますので参考にして下さい。
DFMEA製造・組み立て性の例
製造・組み立ての技術的、物理的限界を考えます。
例)
- 金型に必要な逃げ勾配
- 表面仕上げの能力限界
- 組み立てスペース(例:工具を入れる隙間)
- 公差/工程能力/工程性能
DFMEAサービス性(メンテナンス)の例
製造が市場での使用段階に入った時のサービスおよびリサイクル上の技術的、物理的限界を考えます。
例)
- 工具を入れる隙間
- 故障診断能力
- 材料分類記号(リサイクル用)
- 製造工程で使われている材料/化学物質
DFMEAの発生度&検出度評価基準案(フォーマット)
また、DFMEAでは、故障などの発生度、検出度において、評価基準(案)を設けます。
一例として参考にしてください。
DFMEA発生度評価基準(案)フォーマット
故障の起こりにくさ | 基準:原因の発生‐DFMEA
(部品/車両の故障寿命/信頼性) |
基準:原因の発生‐DFMEA
(部品/車両毎の発生) |
ランク |
非常に高い | 経験のない新技術/新設計 | >100/1000
>1/100 |
10 |
高い | 新設計、新規適用または負荷サイクル/使用条件の変更により故障は避けられない | 50/1000
1/20 |
9 |
新設計、新規適用または負荷サイクル/使用条件の変更により故障は起こりうる | 20/1000
1/50 |
8 | |
新設計、新規適用または負荷サイクル/使用条件の変更により故障は不透明 | 10/1000
1/100 |
7 | |
中程度 | 類似設計や設計シュミレーション/テストの結果で頻繁な故障 | 2/1000
1/500 |
6 |
類似設計や設計シュミレーション/テストの結果で時折り故障 | 0.5/1000
1/2000 |
5 | |
類似設計や設計シュミレーション/テストの結果で単発の故障 | 0.1/1000
1/10000 |
4 | |
低い | ほとんど同じ設計や設計シュミレーション/テストの結果でまれな故障 | 0.01/1000
1/100000 |
3 |
ほとんど同じ設計や設計シュミレーション/テストの結果で故障は観察されない | <0.001/1000
1/1000000 |
2 | |
非常に低い | 予防管理で故障は除去されている | 予防管理で故障は除去されている | 1 |
DFMEA検出度評価基準(案)フォーマット
検出の機会 | 基準:設計管理による検出可能性 | ランク | 検出可能性 |
検出の機会なし | 設計管理なし:検出できないまたは解析されない | 10 | ほとんど不可能 |
いかなるステージにおいても検出不能 | 設計解析/検出管理は検出能力が弱い:仮想解析(例:CAE、FEAなど)は実際の作動条件に相関がない | 9 | 非常に困難 |
量産出図以降で量産開始前 | 量産出図以降で量産開始前段階での製品検証/妥当性確認が合否判定のみ
(サブシステムやシステムで故障が起こるまでテストする、システム相互作用テストなど) |
8 | 困難 |
量産出図以降で量産開始前の故障限界テスト
(サブシステムやシステムで耐久性試験後の機能チェックなど)による製品検証/妥当性確認 |
7 | 非常に低い | |
量産出図以降で量産開始前の劣化テスト
(サブシステムやシステムで耐久性試験後の機能チェックなど)による製品検証/妥当性確認 |
6 | 低い | |
量産出図前 |
量産出図前の合否判定テスト(例:性能、機能、チェック等)による製品妥当性確認(信頼性テスト、開発、妥当性確認) | 5 | 中程度 |
量産出図前の故障限界テスト(例:漏れ、座屈、クラック等)で製品妥当性確認(信頼性テスト、開発、妥当性確認) | 4 | ある程度高い | |
量産出図前の劣化テスト(例:データの傾向、テスト前後の値等)で製品妥当性確認(信頼性テスト、開発、妥当性確認) | 3 | 高い | |
仮想解析‐相関 | 設計解析/検出管理が強い検出能力をもっている
量産出図前の仮想解析(例:CAE、FEA等)が現実のまたは予想されている作動条件に高い相関がある |
2 | 非常に高い |
検出は適用されない:故障の予防 | 設計処置(例:実証済みの設計標準、ベストプラクティス、共通の材料等)により故障原因やモードが完全に除去されている | 1 | ほぼ確実 |
DFMEAとFMEAとの違いとは?やり方やフォーマット&基準例まとめ
DFMEAとは、D:design(設計)段階でのFMEAを指す(Design Failure Mode and Effects Analysisの略)
DFMEAでは、故障などの発生度、検出度において、評価基準(案)を設ける
DFMEAの範囲決定のポイント
ポイント
- 製品はどのような工程、はめ合わせる相手部品またはシステムとインターフェースがあるのか?
- ほかのコンポーネントやシステムに影響を及ぼす製品の機能や特性は?
- 製品の意図した機能を達成するのに必要なほかのコンポーネントやシステムからのインプットはあるのか?
- 連結されたほかのコンポーネントやシステムの潜在故障モードを予防または検出する製品機能はあるのか?
以上です。
ありがとうございました。