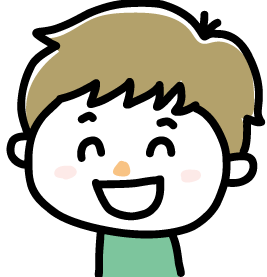
今回のテーマは【FMEA】
品質や工程管理における基礎知識について解説していきますのでぜひどうぞ!
目次
FMEAとFTAの違いとは?故障モード影響度解析やリスクアセスメントの手順
まずFMEAとは、品質管理などにおける【故障モード影響解析】のことであり、一般的には「ボトムアップ法」と呼ばれています。
Failure Mode and Effects Analysisの略です。
アメリカのグラマン社が新しいジェット戦闘機の開発において、油圧機器を用いた操縦システムの信頼性を評価する方法として、この解析方法を採用したと言われています。
大きな問題をはっせいさせる要因がどこに潜んでいるのかを摘出する手法で、故障率の高い故障モードを設計変更により未然に除去することができます。
そしてFMEAと合わせて知っておきたいのが【FTA】です。
FTAとは、故障の木解析:Fault Tree Analysisの略称。
初めに望ましくない事象を定義し、その事象を発生させる要因を摘出する手法で、【トップダウン解析手法】とも呼ばれています。
またシステムの故障を発生させる事象との因果関係を論理記号を利用して、木の枝のようなFT図(Fault Tree Diagram)をつくります。
さらに各事象ごとの故障率を割り当てていくことで、システムに悪影響を及ぼしている事象を抽出していく方法とも言えます。
FMEA | FTA |
品質管理などにおける【故障モード影響解析】のことであり、一般的には「ボトムアップ法」と呼ばれている
大きな問題をはっせいさせる要因がどこに潜んでいるのかを摘出する手法で、故障率の高い故障モードを設計変更により未然に除去することができる Failure Mode and Effects Analysisの略称 |
初めに望ましくない事象を定義し、その事象を発生させる要因を摘出する手法で、【トップダウン解析手法】とも呼ばれている
各事象ごとの故障率を割り当てていくことで、システムに悪影響を及ぼしている事象を抽出していく方法 故障の木解析:Fault Tree Analysisの略称 |
一方で、FT図作成に必要な記号と名称は以下のとおりです。(図解参照)
事象 | 基本事象などの組み合わせによって起こる個々の事実 |
ORゲート(オアゲート) | 入力事象のうち、いずれかひとつが存在するときに出力事象が発生する(論理和) |
ANDゲート(アンドゲート) | すべての入力事象が共存するときのみ出力事象が発生する(論理積) |
基本事象 | これ以上は展開されない基本的な事象 |
工程FMEAの流れ・手順
工程FMEAとは、FMEAの考え方を製造や機械などの工程管理に応用したものです。
工程FMEAの流れはこんな感じ 🙂
工程FMEAの流れ
- 工程ごとに作業を分類し動作レベルに細分化
- 各動作ごとに発生しうるミスを想定し故障モードを決定
- 故障モードに付随する項目を分析・評価
- 改善案を作成し実行
FMEA➀工程ごとに作業を分類し動作レベルに細分化
エクセルなどで作業を分類した一般的な項目は以下のとおりです。
作業項目
- 工程
- 作業名目
- 具体的作業
- 想定されるミス
- 故障モード
- 故障による影響
- 影響度
- 故障の発生原因
- 発生度
- 故障の検出方法
- 検出度
- RPN(影響度×発生度×検出度)
ある工程で行われる作業を大きなくくりで分類します。「工程」と「作業名目」に、例えば「組立」などと記入しましょう。
次に作業内の動作それぞれを洗い出します。
具体的作業に「部品①を製品本体に取り付ける」などと記入します。
FMEA②各動作ごとに発生しうるミスを想定し故障モードを決定
続いて「想定されるミス」「故障モード」の項目を埋めましょう。
例えば「部品のずれ」がミス、「対象部分の接触不良」が故障モードといった具合です。
分類した作業ごとに、これらの項目を記入してください。
このときに大切なのは、工程のミスに起因する故障モードのみを考えることです。
もし「部品①と接合部の形が合致しない」ならばそれは設計上のミスとなり、工程FMEAにおける故障モードとは見なしません。
FMEA③故障モードに付随する項目を分析・評価
故障モードに付随する項目を分析・評価をしていきます。
分析・評価項目
- 故障による影響・影響度
- 故障の発生原因・発生度
- 故障の検出方法・検出度
- RPN
影響度
故障による影響度を10段階で評価!
影響度は、故障による影響の大きさによって以下のように分類します。
⑩まったく機能しない
⑨特定の条件下で機能しない
⑧機能しないおそれがある
⑦特定の条件下で機能が低下する
⑥機能が低下するおそれがある
⑤機能はするが、改善が不可欠
④機能はするが、改善すべき
③影響はないと見なせる
②完全に無視できる程度の影響しかない
①まったく影響がない
また、フォーマットの「故障による影響」の項目には、具体的な影響を記入してください。
たとえばテレビのスクリーンがまったく機能しないような場合には、「画面が映らない」と記入します。
発生度
発生度とは、故障が発生する頻度のことです。
発生頻度に応じた10段階での評価はこんな感じ。
⑩毎回
⑨1日1回
⑧1週間に1回
⑦2週間に1回
⑥1ヶ月に1回
⑤6か月に1回
④1年に1回
③3年に1回
②5年に1回
①発生しない
故障の発生原因」の項目には、そのミスを誘発する要因を記入します。(例:部品AとBが似ているなどが当てはまる)
検出度
検出度とは、検出できる確率のことで、以下のように10段階に分けられます。
⑩検出不可
⑨工程での検出率=10%
⑧工程での検出率=20%
⑦工程での検出率=30%
⑥工程での検出率=50%
⑤工程での検出率=70%
④後の工程で検出率=100%
③次の工程で検出率=100%
②作業途中で検出可能
①作業途中で検出率=100%
フォーマットの「故障の検出方法」の項目には、具体的な検出方法を記入してください。(例:「部品取り付け後、目視確認する」などが該当)
ただし人間が確認する場合、検出率は100%になりませんのでご注意を!
100%としてよいのは、機械で検出する場合のみです。
そして評価した影響度・発生度・検出度を掛け算し、その値はリスクの大きさを示す指標で、RPNと呼ばれます。
RPN=影響度×発生度×検出度
例えば「影響度=6」「発生度=2」「検出度=5」のとき、「RPN=6×2×5=60」となります。
FMEA④改善案を作成し実行
ここまでのステップで明らかにしたRPNをもとに、対処すべき問題に優先度付けを実施し、優先度の高いものから改善を目指しましょう。
ここでいう改善とは、RPNを低下させること!
そのためには影響度・発生度・検出度を下げる取り組みが必要になりますが、影響度を下げることは不可能といえます。
工程を改善しても、その工程で目的とする成果物が同じである以上、そこに異常が生じたときの影響は変化しないからです。
もし、作業の改善である部品の取付ミスの発生頻度が減ったとしても、取付ミスをした際に生じる影響は変わりません。
したがって発生度・検出度の数値の低下が目的です。
ミスの誘発要因を取り除いたり、精度の高い検出機器を導入したりしてみるのが一般的でしょう。
改善策を実施したら、再度RPNを算出して評価します。
RPNが100未満になるまでこれをくり返してください。
FMEAとFTAの違いとは?故障モード影響度解析やリスクアセスメント手順まとめ
FMEAとFTAの違い
FMEA | FTA |
品質管理などにおける【故障モード影響解析】のことであり、一般的には「ボトムアップ法」と呼ばれている
大きな問題をはっせいさせる要因がどこに潜んでいるのかを摘出する手法で、故障率の高い故障モードを設計変更により未然に除去することができる Failure Mode and Effects Analysisの略称 |
初めに望ましくない事象を定義し、その事象を発生させる要因を摘出する手法で、【トップダウン解析手法】とも呼ばれている
各事象ごとの故障率を割り当てていくことで、システムに悪影響をお呼びしている事象を抽出していく方法 故障の木解析:Fault Tree Analysisの略称 |
工程FMEAの流れ
- 工程ごとに作業を分類し動作レベルに細分化
- 各動作ごとに発生しうるミスを想定し故障モードを決定
- 故障モードに付随する項目を分析・評価
- 改善案を作成し実行
以上です。
ありがとうございました。